Optimize productivity: identify process weaknesses and eliminate bottlenecks!
by Veronika Altenbach
Efficient business processes are crucial to a company's success. However, hidden weaknesses often lead to wasted time, unnecessary resource expenditure and higher costs. Various proven methods are available to identify and systematically eliminate such problems. In this article, we list the most effective approaches – including modern process analysis with visual models, bottleneck analysis, value stream analysis and more.
Methods for identifying process weaknesses
A contemporary method for identifying process weaknesses is modeling with BPMN (Business Process Model and Notation). This standardized notation enables a precise and uniform visualization of business processes, making it easier to identify inefficient or redundant steps.
- Process modeling with BPMN: BPMN provides a detailed graphical representation of processes, including all activities, decision points and roles involved. This makes it possible to systematically identify bottlenecks, redundant work and unnecessary delays.
- Flow-oriented analysis: BPMN diagrams are used to map the process flow in a structured and logically comprehensible way. This makes it easier to understand complex processes and helps to exploit optimization potential in a targeted manner.
Using BPMN gives companies a clearer view of their business processes and enables them to make data-based decisions to increase efficiency.
In our article: “Process visualization – the optimal software choice”, we present suitable tools for visualizing your workflows – based on the internationally recognized BPMN 2.0 standard.
Bottleneck analysis
Bottlenecks are one of the most common causes of delays and inefficiencies in business processes. They occur when a particular process step slows down the entire workflow, whether due to limited capacity, inefficient use of resources or excessive waiting times. Bottleneck analysis helps to systematically identify and eliminate these critical bottlenecks.
Important methods for bottleneck analysis:
- Measure throughput times: Record the duration of each process step to identify delays and waiting times.
- Capacity analysis: Compare the maximum capacity of individual process steps with their actual utilization to identify overloads at an early stage.
- Bottleneck simulation: Use of simulation tools or process models to predict potential bottlenecks under different conditions.
Once bottlenecks have been identified, companies can take targeted optimization measures – for example, by increasing resources, automating or restructuring the workflow to sustainably increase efficiency.
Value Stream Mapping
This method comes from lean management and looks at all the activities in a process to identify the steps that do not add value. By distinguishing between value-adding and non-value-adding activities, unnecessary delays and inefficiencies can be eliminated in a targeted manner.
- Step 1: Process mapping – First, the current process is visualized as a value stream diagram that includes all relevant activities, material flows and information flows.
- Step 2: Value added analysis – In this step, the individual process steps are evaluated to determine which activities deliver real added value and which are redundant or inefficient.
- Step 3: Identify opportunities for improvement – By identifying non-value-adding activities, targeted optimization measures can be developed, such as reducing waiting times, improving workflows or automating processes.
- Step 4: Implementation and monitoring – The optimizations developed are implemented and continuously reviewed to ensure that the value stream is sustainably improved.
Value stream analysis enables companies to optimize processes, shorten throughput times and work more efficiently overall.
Pareto analysis (80/20 rule)
The Pareto analysis is based on the Pareto principle, also known as the 80/20 rule. This principle states that in many cases 80% of problems are caused by only 20% of the causes. The aim of the Pareto analysis is to identify the most important causes of problems and to eliminate them in a prioritized manner.
- Step 1: Data collection – Collect data on the problems that arise and their frequency or impact.
- Step 2: Sorting the causes – The identified problems are sorted according to their frequency or the damage caused.
- Step 3: Create a Pareto diagram – A graphical representation showing which causes have the greatest impact on the overall problem.
- Step 4: Prioritize actions – By focusing on the few main causes, large improvements can be achieved with little effort.
This method is often used in quality management, process optimization and problem solving to identify the most efficient approaches to solutions and to take targeted measures for improvement.
Ishikawa diagram (fishbone analysis)
The Ishikawa diagram, also known as a fishbone diagram or cause-and-effect diagram, is a tool for analyzing the causes of problems. It helps to identify systematic weaknesses by presenting various influencing factors in a structured way. The diagram resembles a fishbone, with the main categories acting as the “bones” of a central problem.
- Step 1: Define the problem – First, the problem to be analyzed is clearly defined and placed at the top of the fishbone diagram.
- Step 2: Identify the main categories – The possible causes of the problem are divided into overarching categories, typically: people, machines, methods, materials, environment and measurements.
- Step 3: Detailed cause analysis – Within each category, specific influencing factors that could cause or exacerbate the problem are identified.
- Step 4: Analysis and prioritization – Discussion and data analysis are used to highlight the most likely causes, in order to define targeted improvement measures.
Benchmarking
A comparison with best practices in the industry or internal benchmarks can show where your own processes are inefficient and how they can be optimized.
Conclusion
Identifying process weaknesses is crucial for increasing a company's efficiency and competitiveness. Methods such as bottleneck analysis, value stream mapping or Ishikawa diagrams provide structured approaches for systematically detecting and eliminating bottlenecks and inefficiencies. By regularly reviewing and optimizing their processes, companies can sustainably improve their productivity.
Do you want to eliminate bottlenecks and make your business processes more efficient?
Insights for digital decision-makers
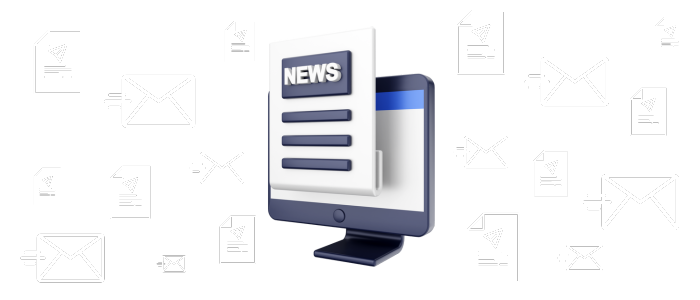